There's much more to Performance Plastics than injection moulding.
Quality Experience Automation Statistical process control Part decoration Additive manufacturing Ultrasonic welding Assembly services Machine vision Reporting ISO 9001:2015 Equipment Efficiency Mould Flow Warehouse management software Design Value Integrityabove all else.Drive growth by choosing a manufacturing partner with
all the right technologies.Choose a partner that's close to your customers.
Over 50 million people, and countless businesses
located within our commercial driving window.From PLA to reinforced nylon. Prototypes to production.
Near limitless 3D printing.In house.Modern engineering resins can satisfy 95% of application requirements.
We use advanced additives to satisfy the remaining 5%.
Injection Moulding
A Trusted Injection Moulder Since 1985
Offering a wealth of experience and value.
We understand that finding an injection moulding partner that meets all your requirements can be very difficult. But it doesn’t have to be, because you just found one.
We’ve spent almost 40 years learning from our customers’ needs and developing systems and technologies to address them. It’s safe to say that after such a long time we’ve gotten pretty good at it.
- A roster of 80 - 450-ton presses, with the bulk being hybrid or all electric
- Broad implementation of factory floor technologies
- Highly developed quality assurance system
- End to end product traceability
- Robust inventory control and WMS
- Advanced scheduling and forecasting
- Over 20 years of continuous ISO certification
- Facilities and staff to handle any volume requirement
- Some of the most experienced and knowledgeable individuals in plastics
Whatever your industry, or however challenging the project, you can count on Performance Plastics for consistency, quality, and a strong commitment to your business.
Please contact us for more information, or to arrange an in-person meeting to discuss your application.
Plastic Assembly
Comprehensive Plastic Assembly Services
Another way we add value for our customers.
We offer comprehensive, and cost-competitive assembly services for companies seeking a single-source solution. Whether you need a dedicated line or cost-saving assembly at the machine, we can help.
Like all services we offer, the quality of our assemblies is strictly controlled, and benefits from the same technologies that our moulding operation benefits from.
Choosing Performance Plastics for moulding, component procurement, and assembly means our customers benefit from the value of streamlined production. We deliver complete assemblies, or sub-assemblies ready for integration.
Contact us today to see how we can help.
Additive Manufacturing
Commercial 3D Printing
For low volume part production, tooling, and fixtures.
Performance Plastics' commercial Fused Filament Fabrication (FFF) process uses an advanced independent dual extruder system to build very large parts in almost any production material.
Like everything else we do, the implementation of our 3D printing solution was built around the needs of our customers:
- Parts and fixtures made from carbon fiber reinforced nylon offer strength comparable to aluminum and can be built in hours.
- An available build volume of 15.75 x 13.75 x 19.50" to print very large parts, or large batches of smaller parts.
- All metal, high temperature (680 °f) extruders paired with synthetic diamond nozzle tips allow the printer to process filled and unfilled production grade thermoplastics without dimensional degradation.
- Where material compatibility allows, we can “over-mould” soft touch materials on rigid substrates.
- Independent dual extruders cut production time in half, making short runs in production thermoplastics more affordable.
- A dedicated desiccating dryer ensures materials are dried to manufacturer specifications and that printed parts exhibit their intended physical characteristics. The drying unit is also used to anneal parts that benefit from heat treating.
- A fully enclosed, temperature-controlled build chamber improves dimensional stability and build quality for resins that require such an environment.
- For electronic security reasons, our commercial printer is operated on a private, air-gapped network.
Production parts can be printed in a wide variety of resins (ISO Tensile bars available on request):
- PETG
- Unfilled Nylons (PA6, PA66, PA612)
- Reinforced Nylons (GF and CF)
- ABS
- Polycarbonate
- Many more including blends and reinforced variations of the above
Decades of experience working with these same resins in a traditional moulding environment is highly transferable to the 3D printing space. It’s given us insights into part performance that you just can’t find elsewhere.
Please give us a call to arrange a meeting – we would love the opportunity to discuss your application. (416) 292-7765.
Ultrasonic Welding
Professional Ultrasonic Welding Services
Ready for the toughest challenges
Performance Plastics offers ultrasonic welding as a stand-alone service, or more commonly as a complimentary service in projects that also include injection moulding and assembly.
We are flexible enough to enter at any stage of a project’s development and will work in tandem with client teams by:
- assisting those clients that are unfamiliar with best practices, guiding them from concept to production.
- evaluating and refining existing designs to optimize ultrasonic welding performance before reaching production.
- developing innovative solutions for production processes that are struggling with quality and consistency.
- supplying production volumes of high-quality assemblies from our facility.
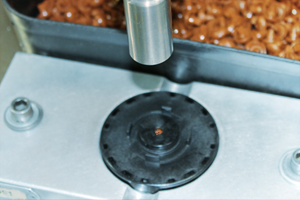
With close to 40 years of experience in the field, and countless successful projects under our belt, you will be hard pressed to find a better ultrasonic welding partner than Performance Plastics Limited.
If you're interested in learning more, we’ve taken the time to produce some technical resources:
How Ultrasonic Welding WorksAn ultrasonic welding process uses high-frequency ultrasonic acoustic vibrations to create a solid-state weld between two materials. Mating parts are held together under pressure and subjected to ultrasonic vibrations usually in the range of 20-40 kHz. The vibrations generate frictional heat at the interface of the parts, which causes the material to soften or melt and form a bond. The process is efficient and a permanent bond is typically formed in less than 1 second. Ultrasonic welding is commonly used in a variety of industries including automotive, medical, and electronics manufacturing, for tasks such as assembling plastic components, sealing containers, or joining wiring. However, ultrasonic welding does have limitations. It is best suited for small to medium-sized parts and may not be as effective for larger, more complex assemblies. It also requires specific joint designs to direct the ultrasonic energy properly, and the materials being welded must be compatible with the process. Most ultrasonic welding applications require custom tooling in the form of a nest (holding fixture to align the mating parts during welding) and a horn (the acoustically tuned tool that ultimately transfers the energy from the welder to a workpiece). While this combination is generally less expensive than other types of custom tooling, it is significant enough to mention here, and can take many weeks to produce. Pros + Cons of Ultrasonic WeldingWhile ultrasonic welding is a precise and efficient method for joining materials, its effectiveness can depend on the specific application, material compatibility, and the skill level of the operators. Some of the pros and cons of the process are detailed below. Pros:
Cons:
We would be happy to discuss ultrasonic welding's suitability for your application. Ultrasonic Welding Joint DesignA well thought-out and implemented joint design is the foundation all successful welds are built on. The configuration of the components to be joined determines how the energy will be directed, how the parts will align, and ultimately, the strength and appearance of the resultant weld. Most joint designs incorporate an energy director - a strategically placed (usually triangular) feature that concentrates the ultrasonic energy:
When an ultrasonic welding joint is designed correctly, ultrasonic energy is concentrated where it's needed most, guaranteeing the initiation of the melting process and the formation of a robust, consistent weld. While it's important to identify and incorporate the right joint early in the design phase, we have been very successful retroactively incorporating joints into existing parts. If you're struggling to get the welding results you need, or if you're still trying to determine the best joint for your parts, please give us a call to discuss - (416) 292-7765. |
Part Decorating
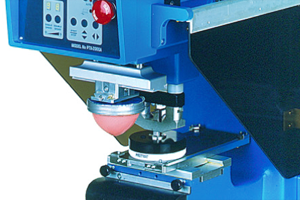
Simple and Efficient Pad Printing
A tried and true method.
To compliment our core services, Performance Plastics Limited's in-house pad printing offers a convenient and straightforward solution for projects that require single-colour part decorations.